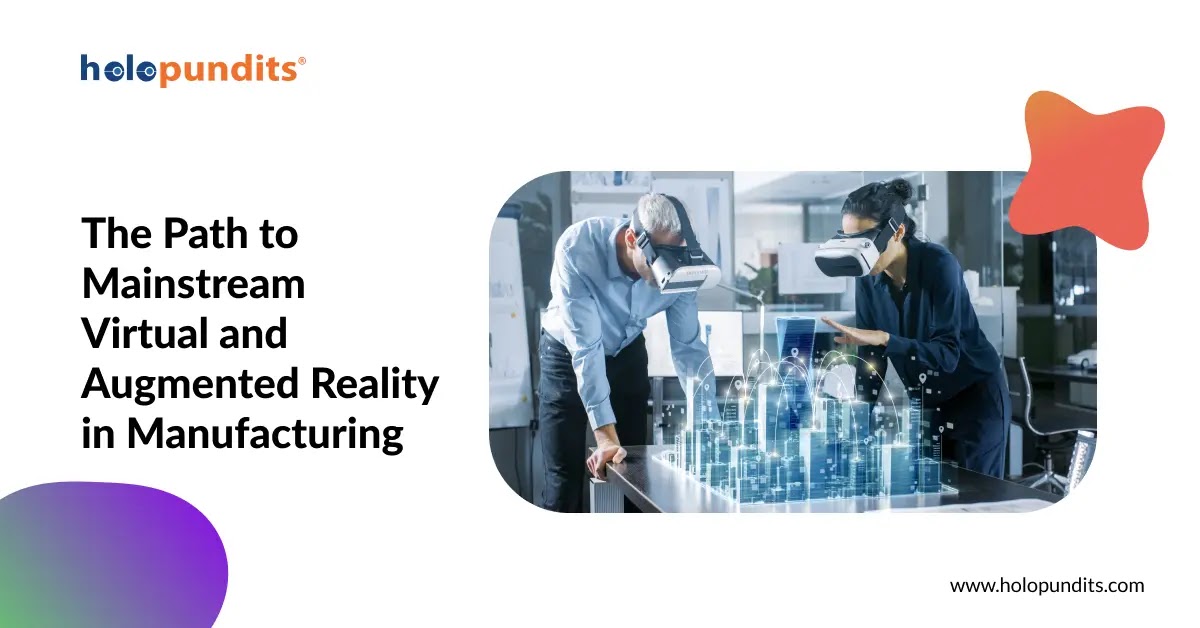
In the world of digital connectedness that we live in today, the development of virtual and augmented reality is a high priority for some of the leading industries that keep the world moving forward. Manufacturers who participated in a PwC survey in 2015 revealed that more than one in three manufacturers would consider, or had plans to adopt virtual and augmented technologies by 2018. (
Source) At this point in 2023, virtual reality in manufacturing is projected to reach USD 14,887 million by 2026. This is a 39.2% increase from where it stood in 2016. (
Source) However, even with this rise in use, there are manufacturers hesitant to adopt the technology into their facilities. With the right knowledge and resources, the path to virtual and augmented reality in manufacturing is clear, if those with the right knowledge and expertise are willing to share valuable information. The truth is that virtual and augmented reality are the perfect tool to help advance manufacturing, and move it in the right direction.
Where can Manufacturers use VR and AR Technology?
Virtual and augmented reality have innate abilities that make the technology well suited to the manufacturing processes and the facilities operation. Some areas that XR technology is being used are:
- Development and product design
- Layout construction
- Remote machine repair
- Inventory management
- Accident prevention and disruption
- Real-time employee instruction and training
Manufacturers can use VR and AR from the very beginning of the design process to the very end to reduce overall cost. Creating diagrams, prototypes, and product designs in virtual or augmented reality enables designers to do initial product testing to determine the benefits of the product before ever spending money on materials. Then, the product can be produced at scale in a facility that has been tailor made to produce high quality items in a layout that makes functional sense. This is made possible with the immersive design features of virtual reality.
Managing inventory and repairing broken down machines is as easy as putting on a pair of augmented reality glasses. If a machine breaks, an on-premises worker can send data via AR to a repairman, enabling repairs to be made faster and more efficiently than before.
Training employees is easier with virtual reality training (VRT) because of the ability of the technology to impart knowledge and internalized information in a natural, active way. Using virtual reality for training and accident prevention purposes reduces overall cost of employment because the training period is faster and more effective than traditional methods. Reduced accidents in warehouses are directly related to the information learned withing training scenarios.
Similarly, there are plenty of reasons manufacturers may want to use VR and AR technology in their facilities:
- Reduction of costs regarding trial and error
- Production quality and speed
- Increased security measures
- Better safety outcomes
The Problems with VR and AR Technology in Manufacturing
Through the years of virtual and augmented reality testing and development, many manufacturers voiced their concerns and reasons why the technology wouldn't be a wise fit for the industry. Here are some of their concerns, and why some manufacturers are still hesitant to make the necessary strides to adopt these beneficial devices.
- Unnecessary equipment for processes that already work
- Too high of an entry cost
- They lack the technology skills to implement
- Benefits of implementation do not outweigh the time and cost
In the same PwC study mentioned in the introduction, those on the fence or ultimately deciding not to adopt VR and AR into their facilities stated cost prohibition and lack of necessity as their main purpose for not entertaining the idea. This is understandable, given the high cost of creating training programs, upfront equipment costs, and the time it takes to familiarize employees with a new equipment. Many find it difficult to justify the expense at all.
Other reasons include the lack of technological skills required to implement, and that the benefits do not outweigh the time and effort required for use. These are also reasonable concerns. After all, the way things have been done in the past will still work for the future. Right? Within reason. However, as more and more manufacturers take the time to introduce AR and VR technology to the industry, it'll become harder and harder to justify this lack of forward thinking.
As the rapid adoption becomes imminent, those refusing to use VR and AR to their benefit will ultimately see competitors advance in the industry, while they themselves stagnate. Operating with outdated technology while others upgrade and move on will lead to doors being permanently closed. Those using XR to build better processes and products will create faster and better products in the long run, and not only justify the time and monetary investment, they'll be grateful for it. They'll make their money back over and over again.
The Path to Getting Virtual and Augmented Reality in Manufacturing Facilities
The adoption of XR technology is a justifiable business expense, one that those willing to utilize will and have already begun to see a rapid return on investment (ROI). This ROI can stem from several sources, like reduced accidents, better training initiatives, and repair help. Getting hesitant companies to commit to the technology is simply a matter of showing that the benefits do outweigh the cost. The path to modernized manufacturing facilities can be broken down into recognizable groups of thought:
Familiarity- By frequently showing the benefits of virtual and augmented reality, as well as their use cases in manufacturing, VR and AR will go a long way in convincing those in charge of operations how the technology will benefit their personal company. Familiarity with the technology will give them a greater understanding of where they can use it.
Assistance- Learning about a new technology can be daunting, and a limiting barrier for entry, but with the rise of XR use cases there has also been a rise in companies willing to share their expertise with the public. These companies develop their services with the user in mind, creating an open knowledge base around an otherwise unfamiliar technology.
Lowered Cost Threshold- While it is difficult to lower the cost of certain items (companies to have to at least make a profit), it is easier to accept the cost of certain things when you realize the benefits that VR and AR have as simple fact of use; not to mention the eventual ROI. Keep in mind that eventually, potentially similar to how computers, cellphones, and other devices have become cheaper, VR and AR devices will follow suit and have a lower entry point for use.
In the end, the major barriers for virtual and augmented reality implementation into manufacturing facilities can be mitigated with the proper resources. Showcasing the benefits of the technology will prove that it does belong in the industry and that each group that does adapt it to their personal use creates a more functional, beneficial environment for their own facility and those they work with. Operating with outdated systems lowers their ability to perform on par with groups of a similar fashion. Staying on top of technological advances will improve systems for everyone.